Filtratiesysteem voor smeltpolymeerfiltratie
Smeltpolymeerfiltratiesysteem
Een smeltpolymeerfiltratiesysteem is essentieel in veel toepassingen waarbij polymeren worden verwerkt of gebruikt, zoals bij de productie van de PET/PA/PP-polymeerindustrie, pre-polymerisatie, eindpolymerisatie, filamentgaren, het spinnen van polyesterstapelvezels, BOPET/BOPP-films of membranen.Dit systeem helpt bij het verwijderen van onzuiverheden, verontreinigingen en deeltjes die de viscositeit beïnvloeden uit het gesmolten polymeer, waardoor de kwaliteit en consistentie van het eindproduct wordt gegarandeerd.
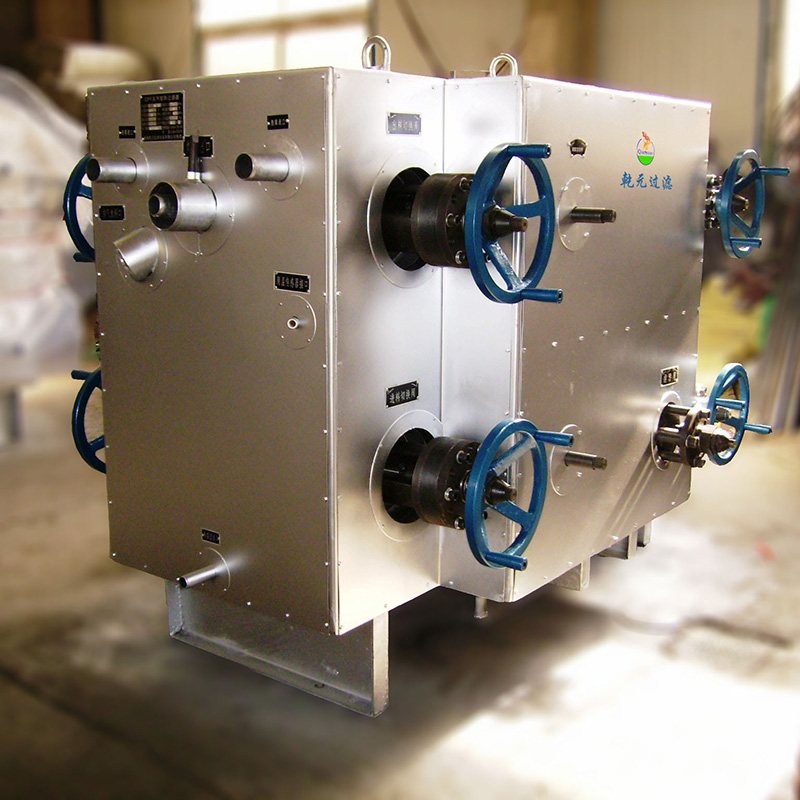
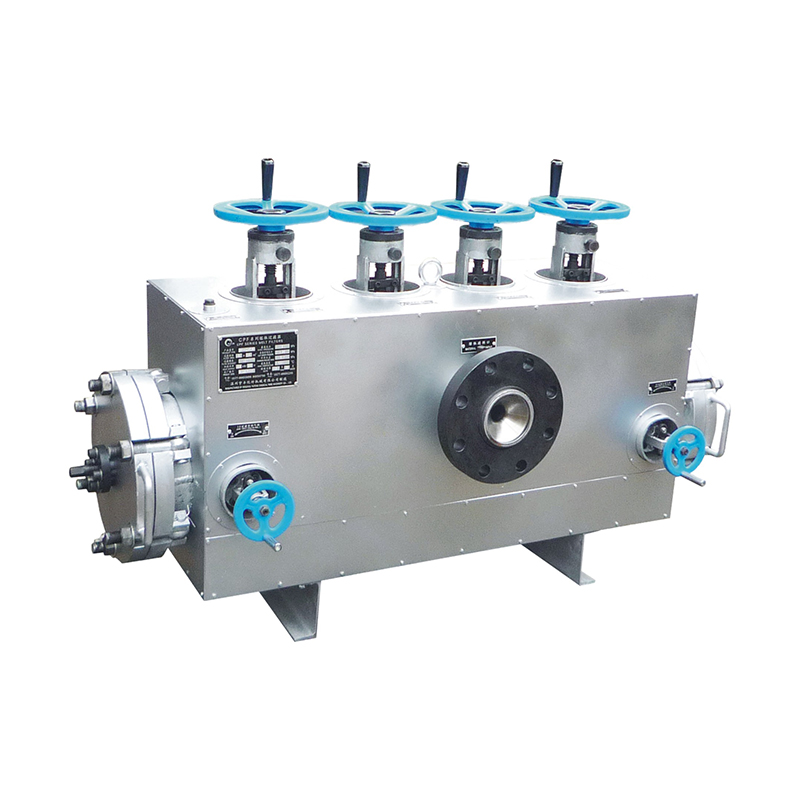
Om de kwaliteit van het smeltpolymeer te verbeteren en de levensduur van de spinpack-componenten te verlengen, is een continu smeltfilter (CPF) op de hoofdsmeltleiding geïnstalleerd.Het kan mechanische onzuiverhedendeeltjes met een diameter groter dan 20-15 μm in de smelt verwijderen en heeft ook de functie om de smelt te homogeniseren.Over het algemeen bestaat het filtersysteem uit twee filterkamers en zijn de driewegkleppen aangesloten op de smeltpijpleiding.De driewegkleppen kunnen periodiek worden geschakeld om het gebruik van de filterkamers af te wisselen en een continue filtratie te garanderen.De behuizing van de filterkamer is uit één stuk gegoten met roestvrij staal.Het filter met groot oppervlak bestaat uit meerdere geplooide kaarsfilterelementen.Het kaarsfilterelement wordt ondersteund door een kerncilinder met gaten en de buitenlaag is uitgerust met een enkel- of meerlaags metalen gaas of gesinterde metaalpoederschijf of meerlagig metalen gaas en gesinterde vezels of gesinterd metaaldraadgaas, enz. in verschillende filtratiesnelheden die gebaseerd zijn op de vereisten van eindproducten.
Over het algemeen zijn er verschillende soorten filtratiesystemen, zoals horizontaal continu filtratiesysteem, verticaal continu filtratiesysteem.Tijdens het spinproces van PET-chips wordt bijvoorbeeld gewoonlijk het verticale filtertype van het kaarstype voorgesteld, dat wil zeggen met een filtratieoppervlak van 0,5 ㎡ per kaarskern.Er zijn veelgebruikte configuraties van 2, 3 of 4 kaarskernen, overeenkomend met filtratiegebieden van 1, 1,5 of 2 ㎡, en de overeenkomstige smeltfiltratiecapaciteiten zijn 150, 225, 300 kg/u.Het verticale filtratiesysteem heeft een grotere omvang en een complexere werking, maar heeft veel voordelen vanuit procesperspectief: (1) Het heeft een grote thermische capaciteit, kleine variaties in de smelttemperatuur en geen dode zones wanneer het materiaal stroomt.(2) De structuur van de isolatiemantel is redelijk en de temperatuur is uniform.(3) Het is handig om de filterkern op te tillen wanneer u het filter verwisselt.
Het drukverschil voor en na het nieuw gebruikte filter is laag.Naarmate de gebruiksduur toeneemt, raken de gaten van het filtermedium geleidelijk verstopt.Wanneer het drukverschil de instelwaarde bereikt, bijvoorbeeld bij het draaien van PET-chips, is het cijfer doorgaans ongeveer 5-7 MPa, en moet de filterkamer worden omgeschakeld.Wanneer het toegestane drukverschil wordt overschreden, kan het filtergaas worden gedraaid, neemt de maaswijdte toe en neemt de filtratieprecisie af totdat het filtermedium wordt gescheurd.De geschakelde filterkern moet vóór hergebruik worden gereinigd.De helderheid van het effect kan het beste worden bepaald door het "bellentest"-experiment, maar kan ook worden beoordeeld op basis van het drukverschil voor en na het nieuw geschakelde filter.Over het algemeen mag het kaarsenfilter niet meer worden gebruikt als het 10-20 keer is gescheurd of gereinigd.
Voor filters uit de Barmag NSF-serie worden ze bijvoorbeeld verwarmd door bifenylstoom in de mantel, maar de temperatuur van de warmteoverdrachtsvloeistof mag niet hoger zijn dan 319 ℃ en de maximale bifenylstoomdruk is 0,25 MPa.De maximale ontwerpdruk van de filterkamer is 25 MPa.Het maximaal toegestane drukverschil voor en na het filter bedraagt 10 MPa.
Technische parameters
Model | L | B | H | H1 | H2 | FIX(H3) | Inlaat en uitlaat DN (Φ/) | Filtergebied (m2) | Toepasselijke schroefstang (Φ/) | Ontworpen stroomtarief (kg/u) | Filterbehuizing | Filter element | Totaal gewicht (kg) |
PF2T-0,5B | 900 | 1050 | 1350 | Als klantsite | 2200 | 22 | 2x0,5 | 65 | 40-80 | Φ158x565 | Φ35x425x4 | 660 | |
PF2T-1.05B | 900 | 1050 | 1350 | 2200 | 30 | 2x1,05 | 90 | 100-180 | Φ172x600 | Φ35x425x7 | 690 | ||
PF2T-1.26B | 900 | 1050 | 1390 | 2240 | 30 | 2x1,26 | 105 | 150-220 | Φ178x640 | Φ35x485x7 | 770 | ||
PF2T-1.8B | 950 | 1140 | 1390 | 2240 | 40 | 2x1,8 | 120 | 220-320 | Φ235x620 | Φ35x425x12 | 980 | ||
PF2T-1.95B | 950 | 1140 | 1390 | 2240 | 40 | 2x1,95 | 130 | 250-350 | Φ235x620 | Φ35x425x13 | 990 | ||
PF2T-2.34B | 1030 | 1200 | 1430 | 2330 | 40 | 2x2,34 | 135 | 330-420 | Φ235x690 | Φ35x485x13 | 1290 | ||
PF2T-2.7B | 1150 | 1200 | 1440 | 2350 | 50 | 2x2,7 | 150 | 400-500 | Φ260x690 | Φ35x485x15 | 1320 | ||
PF2T-3.5B | 1150 | 1250 | 1440 | 2350 | 50 | 2x3,5 | 160 | 500-650 | Φ285x695 | Φ35x485x19 | 1450 | ||
PF2T-4.0B | 1150 | 1250 | 1500 | 2400 | 50 | 2x4,0 | 170 | 600-750 | Φ285x735 | Φ35x525x19 | 1500 | ||
PF2T-4.5B | 1150 | 1250 | 1550 | 2400 | 50 | 2x4,5 | 180 | 650-900 | Φ285x785 | Φ35x575x19 | 1550 | ||
PF2T-5.5B | 1200 | 1300 | 1500 | 2350 | 50 | 2x5,5 | 190 | 800-1000 | Φ350x755 | Φ50x500x15 | 1650 |